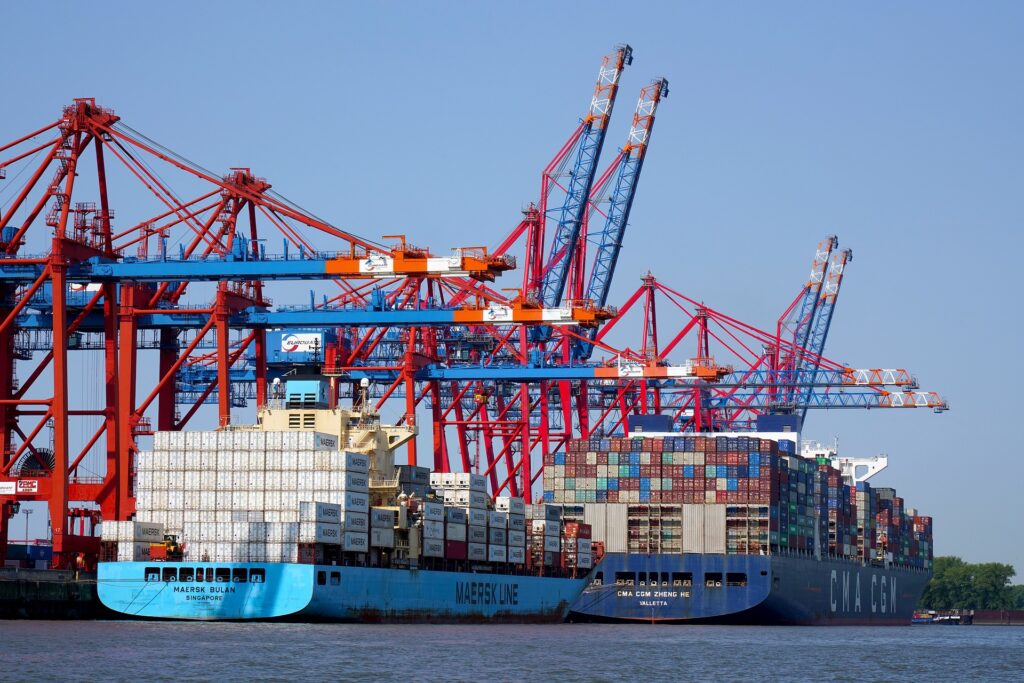
Tariff increases may take effect with top trading partners as early as January 20, 2025 when presidential elect Trump takes office. In late November 2024, plans were announced to impose 25% tariffs on all imported products from Mexico and Canada, and an additional 10% tariff above any existing tariffs on imports from China. This is a reversal of the tariffs proposed during the presidential campaign of a 60% tariff on all goods from China and a 10% tariffs on goods from all other countries.
The president holds ultimate authority to make decisions on trade and tariff policies while relying heavily on key roles within their cabinet. The new administration has appointed a Secretary of the Department of Commerce who will lead the tariff and trade agenda and collaborate with other cabinet members. These roles include working with the U.S. Trade Representative on tariff policies and trade enforcement, and the Secretary of Treasury who helps shape U.S. economic policy, including trade and tariff policies.
During the first Trump presidential term in 2018, approximately 12% tariffs were imposed on goods from China as well as higher tariffs on select goods such as solar panels, washing machines and steel from China. These tariffs were largely extended by the Biden administration, and other changes have been made and continue to be made, such as increases on tariffs on select Chinese goods such as electric vehicles and steel, among other products.
Disruptions to supply chains and sourcing shifts can result from new tariff policies. Since 2018, many U.S. manufacturers and retailers have reduced their dependence on China, shifting their production to other low-wage countries such as Mexico, Vietnam, and India, and are continuing to do so.
With all this in mind, the need for supply chain planning cannot be understated. What are the elements of supply chain planning involving trade and sourcing that can help shippers and their third-party logistics (3PL) providers prepare for the changes ahead?
Here’s a look at key areas of supply chain planning to consider in light of changes in tariffs and trade policies:
Inventory positioning – regionalization
Sourcing issues and inventory imbalances can be some of the biggest fallout from supply chain disruptions to recover from. For these reasons, many manufacturers are sourcing closer to home and hiring producers within their world region. Following the supply chain disruptions of the pandemic, many sectors have experienced a shift back to just-in-time (JIT) inventory strategies due to cost pressures and the requirement to reduce working capital.
Regional U.S. warehousing is on the rise and many manufacturers, distributors and retailers have seen the benefits of decentralized inventories. The age of e-commerce and omnichannel shopping have greatly raised consumer expectations which have spilled over to B2B shipping. Many U.S. companies have adopted strategies to maintain inventory in multiple regions of the country as opposed to one or two facilities.
U.S.-based 3PLs and warehousing companies can help shippers create a more regionalized supply chain, even sourcing components in one region of the U.S. or in North America, and assembling in another, minimizing transportation costs and trade risks.
Managing the global supply chain
The trend toward regionalization is also happening on a global scale. Globalization has a dramatic impact on strategic sourcing and how the supply chain is managed, and the threat of changes in trade policies and tariffs add to the list.
Generally, the more global a supply chain, the greater the likelihood of disruptions from labor strikes, cargo theft, natural disasters or geopolitical conditions. Schedule changes, in-transit delays, service disruptions and carrier bankruptcies are just a few other examples of sourcing, transportation and logistical issues.
A recent McKinsey survey found that two-thirds of global shippers surveyed are developing regional supply networks. The survey found that independent regional supply networks are most prominent in two regions: Europe and Southeast Asia.
There are many digital trade platforms that can help shippers and manufacturers with managing tariffs and trade regulations and the associated documentation. This includes support with streamlining processes and reducing compliance risks. These digital trade platforms include solutions by SAP, Thomson Reuters and others.
Other solutions can help companies track tariff changes, trade regulations, and global market trends so they can react quickly. Software tools include everything from basic spreadsheet software to advanced analytics that use predictive analytics to model demand fluctuations, supply chain disruptions, and potential cost increases under different scenarios. Global shippers, in particular, can use scenario modeling to create simulations that can analyze the impact of various tariff scenarios on their supply chains, allowing for informed decision-making.
Sourcing – diversify your supplier base
As these points suggest, it’s important to mitigate risks associated with tariffs and trade restrictions. Analyzing your supplier base and creating contingency plans is one way to do this. One of the many supply chain lessons learned from the pandemic was the need to diversify supplier bases and explore alternative shipping routes. Identify your most vulnerable products that could be affected by tariffs.
In anticipation of potential increases in tariffs, many companies with U.S. operations are exploring alternative sourcing options, including domestic manufacturing and nearshoring, regional production hubs, and new supplier relationships.
U.S.-based 3PLs have strong networks and can help shippers develop a more regional supply chain, even help identify alternative suppliers in some cases, both domestic and international, to reduce dependence on any single country or region.
Lastly, greater levels of supply chain planning can help U.S. companies to create more resilient supply chains that are secure and diverse to help guard against the uncertainty from shifts in trade policies. As noted in the recently created White House Council on Supply Chain Resilience, characteristics of resilient supply chains include greater domestic production; a diverse and agile supplier base; built-in redundancies; a reliable transportation system; secure critical infrastructure; and adequate stockpiles, among other attributes.